Comparing Welding Types: TIG vs. MIG vs. Stick
Water Problems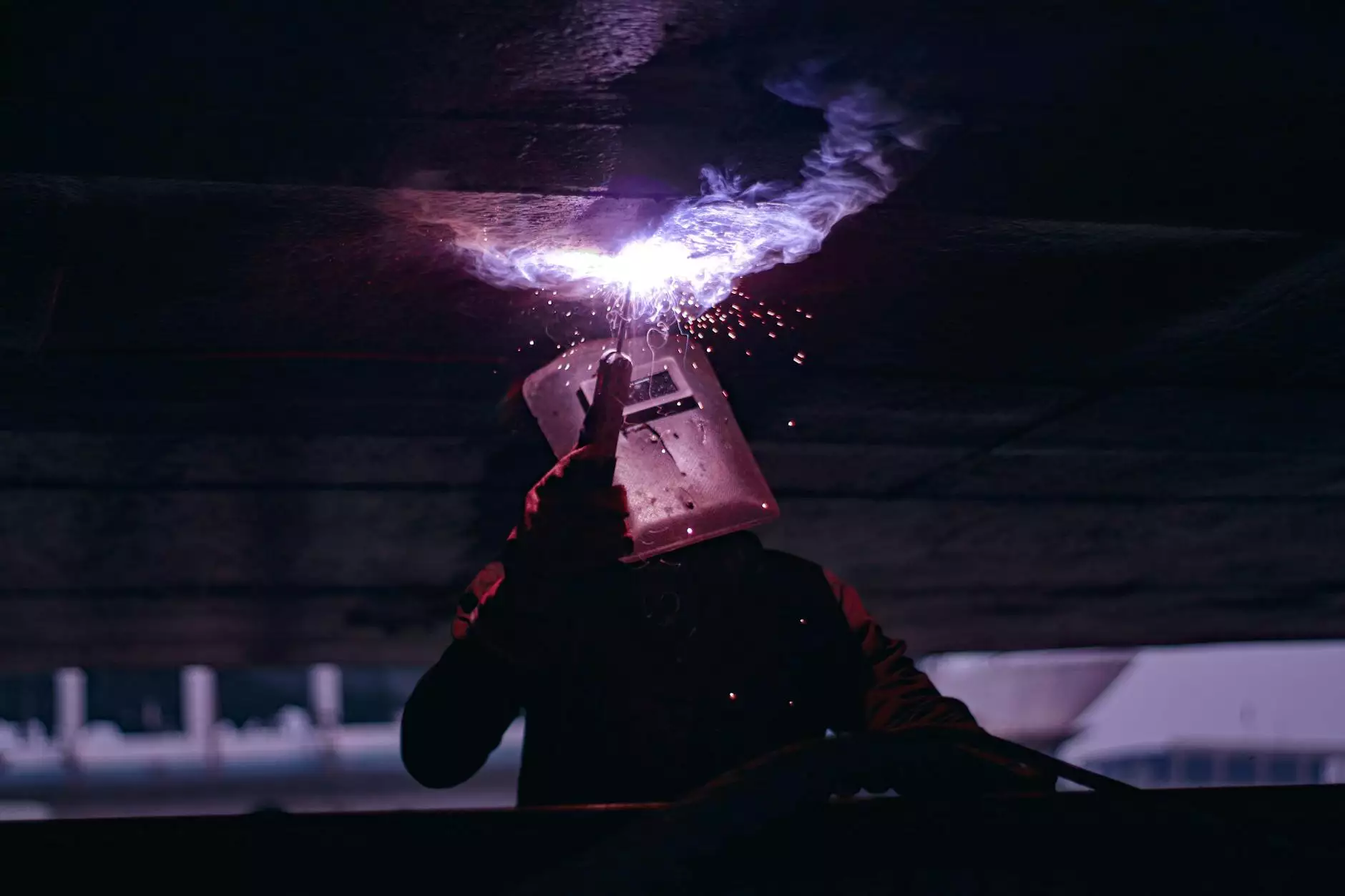
Introduction
Welcome to Parrish Well Drilling's comprehensive guide on comparing welding types! In this article, we will dive into the world of TIG, MIG, and Stick welding. Whether you are a seasoned professional welder or just getting started with welding, understanding the differences between these welding methods is crucial when choosing the right one for your specific needs.
TIG Welding
Tungsten Inert Gas (TIG) welding, also known as Gas Tungsten Arc Welding (GTAW), is a precise and versatile welding method primarily used for welding aluminum, stainless steel, and other exotic metals. TIG welding utilizes a non-consumable tungsten electrode, an inert gas (usually argon), and a separate filler material.
The advantages of TIG welding include its ability to produce high-quality welds with excellent control over heat input, resulting in minimal distortion and a clean appearance. The process allows for welding thin materials and intricate welds, making it suitable for applications such as aerospace, automotive, and artistic metalwork. TIG welding also provides superior weld penetration and precise control over the weld pool.
However, TIG welding is a relatively slow process compared to other welding types. It requires significant skill and dexterity due to the need for manually feeding and controlling the filler material. TIG welding also necessitates a higher level of cleanliness and surface preparation to achieve optimal results.
MIG Welding
Metal Inert Gas (MIG) welding, also referred to as Gas Metal Arc Welding (GMAW), is one of the most common welding methods used in various industries. MIG welding involves the use of a consumable wire electrode, an inert gas (typically argon plus a small percentage of carbon dioxide), and direct current (DC) power.
MIG welding offers several advantages, including its high efficiency and productivity. The continuous wire feed allows for faster welding and reduced downtime. This method is suitable for welding thick materials and provides good versatility across a wide range of metals, including steel, stainless steel, and aluminum.
The simplicity of operation makes MIG welding ideal for beginners, as it requires less manual dexterity and skill compared to TIG welding. It also enables welding in various positions and can be easily automated for mass production.
However, MIG welding may result in lower precision compared to TIG welding, and the weld appearance may not be as clean. It is also more prone to spatter and requires adequate ventilation due to the use of shielding gas. Despite these limitations, MIG welding remains a popular choice for fabrication, automotive repairs, and general metalworking.
Stick Welding
Shielded Metal Arc Welding (SMAW), commonly known as Stick welding, is a traditional welding method widely used in construction, maintenance, and repair applications. Stick welding utilizes a flux-coated electrode (the "stick") that melts and creates a protective gas shield.
Stick welding offers excellent versatility and can be performed in various environments, including outdoor settings and adverse conditions. This method is especially suitable for heavy-duty welding on thick metals, such as steel and cast iron. Stick welding also provides good penetration, making it effective for welding in tight, hard-to-reach areas.
Although Stick welding is more forgiving when it comes to surface preparation, it requires more manual effort and frequent electrode replacement compared to TIG and MIG welding. It may also produce more spatter and require post-weld cleaning. Despite these considerations, Stick welding remains a preferred choice for its ruggedness, portability, and cost-effectiveness.
Choosing the Right Welding Type
When deciding which welding type is best suited for your needs, it is important to consider various factors such as:
- Material type and thickness
- Required weld quality and appearance
- Control over heat input and distortion
- Application complexity and precision
Each welding method has its own strengths and limitations, making it essential to evaluate your specific requirements to make an informed decision.
Conclusion
In summary, TIG, MIG, and Stick welding offer distinct advantages and applications. TIG welding excels in precision and control, making it ideal for specialized industries. MIG welding offers efficiency and versatility, catering to a wide range of materials. Stick welding proves its utility in heavy-duty and rugged conditions.
At Parrish Well Drilling, we understand the importance of selecting the right welding type for your projects. Our experienced welders are skilled in all three methods, ensuring top-quality welds that meet your specific requirements. Contact us today to discuss your welding needs and benefit from our expertise.