Understanding the Role of Custom Mold Makers in Modern Manufacturing
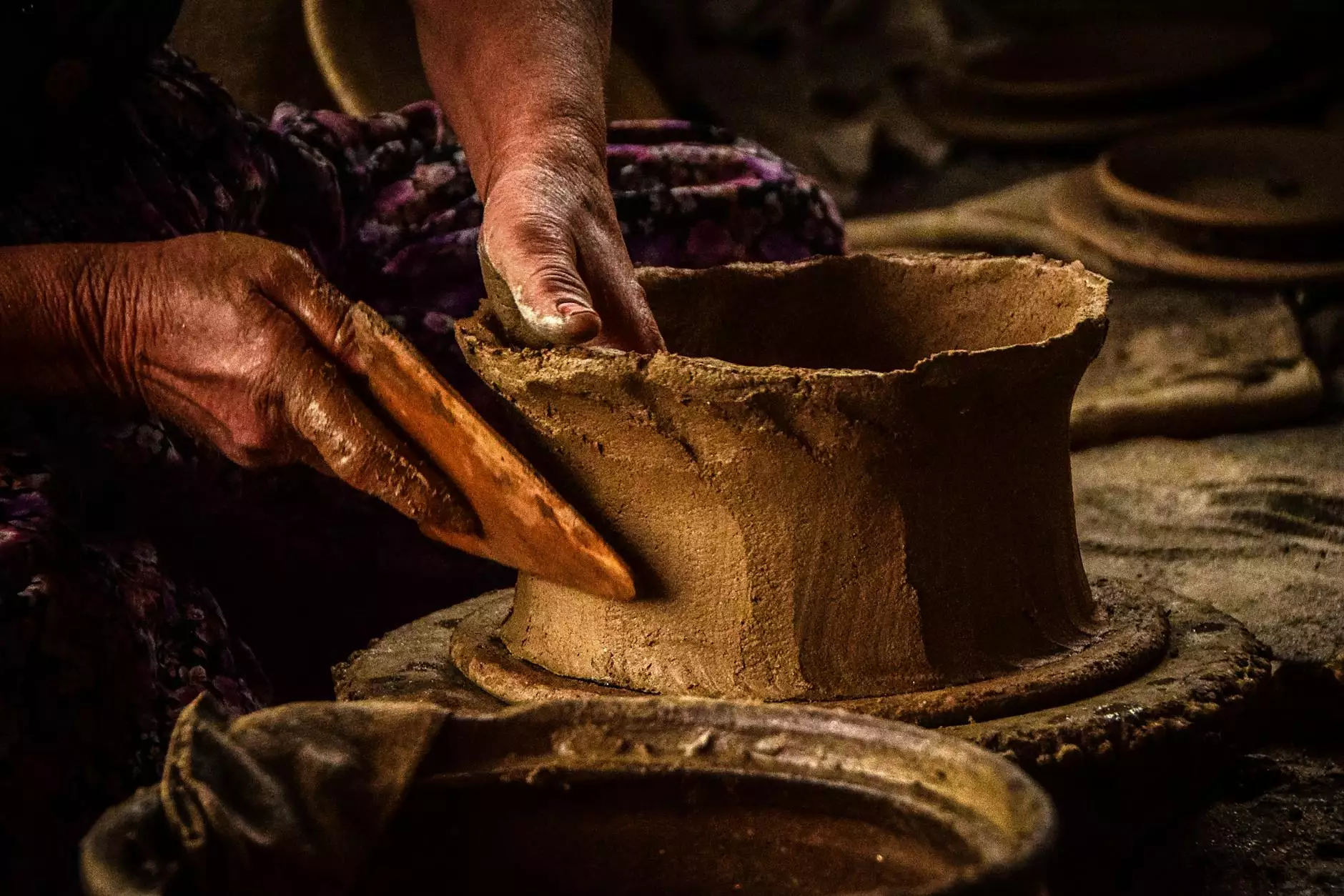
The manufacturing industry continuously strives for innovation, efficiency, and minimal wastage. At the heart of this evolution lie custom mold makers, whose expertise facilitates the production of high-quality components that meet the demanding needs of various sectors. In this extensive article, we will delve into the significance, processes, and benefits of custom mold makers, while ensuring that you understand why they are indispensable to modern manufacturing.
What are Custom Mold Makers?
Custom mold makers specialize in crafting molds tailored to specific product designs and materials. These molds are integral in processes such as injection molding, blow molding, and vacuum forming. The molds created by these experts determine the final shape, size, and finish of the products, making their role crucial in achieving accuracy and efficiency in production.
Key Functions of Custom Mold Makers
Custom mold makers engage in several essential functions that contribute significantly to manufacturing processes. Some of the key responsibilities include:
- Designing Molds: Working closely with engineers and designers, custom mold makers translate product concepts into detailed mold designs.
- Prototyping: Creating prototypes helps test and refine the mold design before full-scale production commences.
- Manufacturing Molds: Utilizing advanced machinery and techniques, they fabricate molds with precision.
- Mold Maintenance and Repair: Regular inspection, maintenance, and repair of molds ensure longevity and effectiveness.
- Collaboration: They work alongside other manufacturing sectors like metal fabricators to integrate diverse materials seamlessly.
The Importance of Precision in Mold Making
In today’s competitive landscape, precision is paramount. Custom mold makers must employ state-of-the-art technology and techniques to ensure that every aspect of the mold aligns with the product specifications. This includes:
- 3D Modeling: Utilizing CAD (Computer-Aided Design) software to create detailed three-dimensional models that provide a clear visual representation of the mold.
- Machining Techniques: Implementing CNC (Computer Numerical Control) machining for high precision and repeatability in mold fabrication.
- Quality Assurance: Rigorous testing and quality checks during the manufacturing process to maintain standards.
Industries That Benefit from Custom Mold Makers
The reach of custom mold makers extends across various industries, each with its unique requirements. Some of the prominent sectors include:
1. Automotive Industry
The automotive industry makes extensive use of custom molds to design various parts such as dashboards, fenders, and other intricate components. Precision in mold making ensures that parts fit perfectly and perform reliably under stress.
2. Consumer Goods
From household items to personal care products, custom mold makers are behind the scenes creating the molds that enable mass production of consumer goods. The ability to create unique designs and shapes caters to evolving consumer preferences.
3. Medical Devices
In the medical field, custom molds are essential for producing components like surgical instruments and implants. The compliance with strict regulations mandates exceptional precision and hygiene in the manufacturing process.
Innovations in Mold Making Technology
The landscape of mold making is constantly evolving, driven by advancements in technology. Some innovations shaping the industry include:
- 3D Printing: Accelerating the prototyping process and reducing lead times, 3D printing allows for rapid adjustments in design.
- Smart Manufacturing: Implementation of IoT (Internet of Things) technology to monitor mold performance and predict maintenance needs, reducing downtime.
- Advanced Materials: Continued research in materials science leads to the use of high-performance polymers and metals that offer improved durability and functionality.
The Process of Custom Mold Making
Understanding the step-by-step process of mold making can enhance your appreciation for the intricate work custom mold makers do:
1. Feasibility Study
The journey begins with a feasibility study to assess the design and materials required for the mold. This step is crucial for determining the viability of the project.
2. Design Development
Certified designers create detailed schematics and CAD models. This phase focuses on every detail to ensure a functional mold design.
3. Prototype Production
Prototyping allows for the testing of the mold design and identifying potential issues before mass production. Adjustments can be made swiftly in this stage.
4. Mold Fabrication
Once the prototype is approved, the fabrication process begins. Techniques like CNC machining and EDM (Electrical Discharge Machining) are employed to create the mold.
5. Testing and Quality Control
Before the mold is put into production, it undergoes rigorous testing to ensure it meets all required specifications. This includes checking for dimensional accuracy, functionality, and overall quality.
6. Production Support
Custom mold makers provide ongoing support during the manufacturing process to address any issues that may arise and to optimize production efficiency.
Benefits of Partnering with Custom Mold Makers
Choosing to work with experienced custom mold makers can yield several benefits for businesses:
- Cost Efficiency: Custom molds, while initially more expensive, reduce production costs in the long run due to fewer defects and reduced waste.
- Enhanced Quality: Precision in mold making leads to superior quality products that meet stringent industry standards.
- Faster Production Times: A well-designed mold streamlines the production process, allowing companies to bring products to market more quickly.
- Customization: Custom mold makers provide tailored solutions that align with specific business needs and product requirements.
Choosing the Right Custom Mold Maker
When it comes to selecting a custom mold maker, understanding their expertise and capabilities is vital. Here are some key factors to consider:
- Experience: Look for mold makers with a proven track record in your industry to ensure they understand the unique challenges you face.
- Technology: Evaluate the technologies and materials they employ to gauge their ability to innovate and maintain quality.
- Customer Support: Choose a partner who prioritizes communication and offers ongoing support before, during, and after mold production.
Conclusion
In the world of manufacturing, custom mold makers serve as the backbone of efficient production processes. Their expertise not only ensures the creation of high-quality components but also facilitates innovation across numerous industries. By understanding the vital role they play and selecting the right partners, businesses can enhance their production capabilities, reduce costs, and improve their market competitiveness.
As the demand for high-quality and customized products continues to rise, the importance of skilled custom mold makers will undoubtedly escalate. Invest in a partnership that emphasizes quality, precision, and innovation to keep your business at the forefront of the industry.