Understanding Dip Molding Materials in Electronics and Medical Supplies
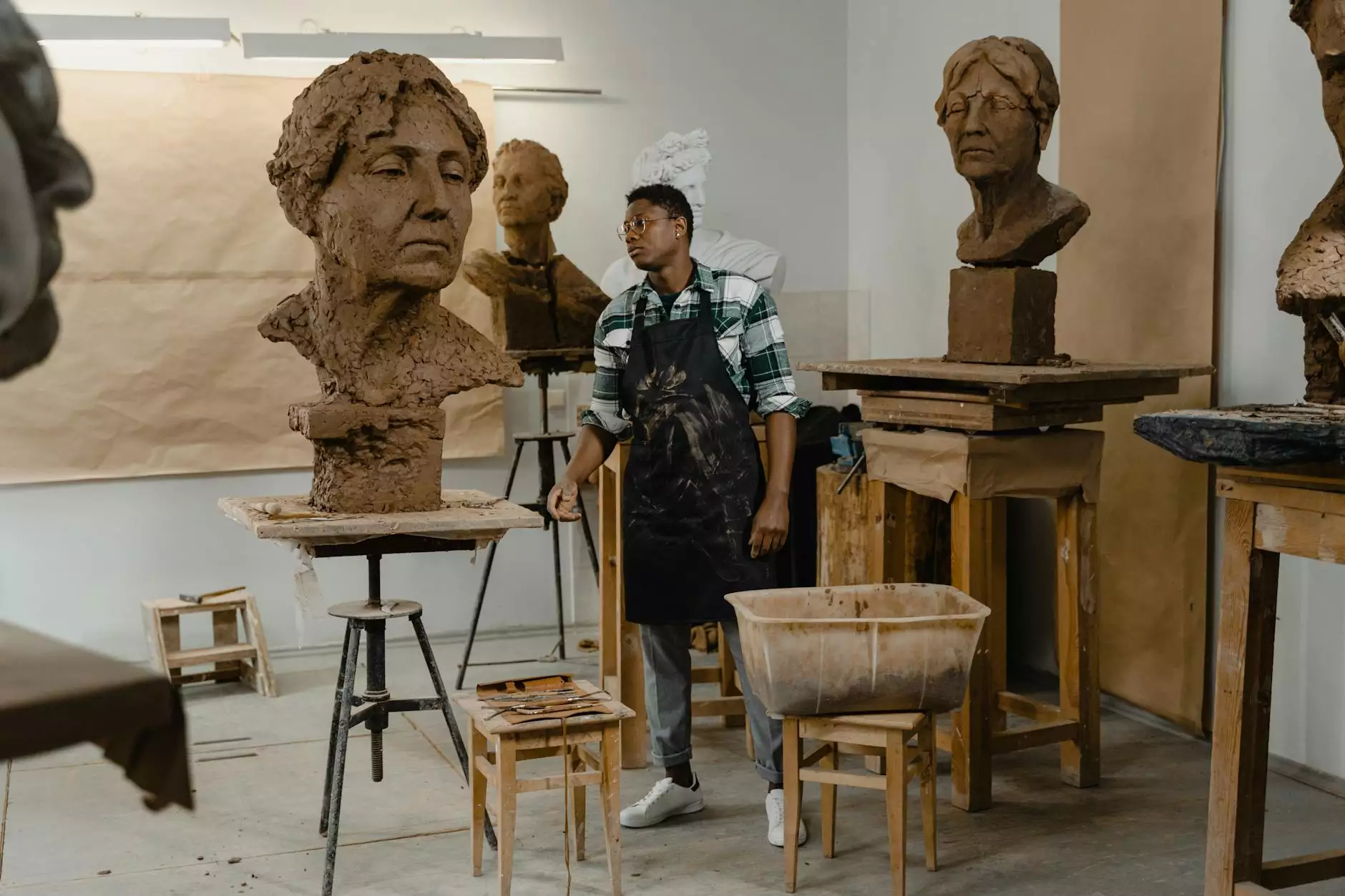
In the contemporary industrial landscape, dip molding materials have emerged as a pivotal player, especially within the realms of electronics and medical supplies. These materials provide significant advantages in terms of flexibility, durability, and cost-effectiveness. This article delves deep into the defining aspects of dip molding materials, their advantages, applications, and future innovations that are set to transform the manufacturing sectors.
What are Dip Molding Materials?
At the core, dip molding is a manufacturing process where a product is formed by dipping a substrate into a liquid material, usually thermoplastic. This technique is widely recognized in various industries, providing robust encapsulation and insulation solutions.
- Thermoplastic Elastomers (TPE): TPEs are often utilized due to their excellent flexibility and durability.
- Polyvinyl Chloride (PVC): PVC is a versatile choice that offers great insulation properties.
- Liquid Silicone Rubber (LSR): Known for its heat resistance and biocompatibility, LSR is frequently used in medical applications.
The Dip Molding Process Explained
The process of dip molding involves several systematic steps that ensure the production of high-quality items:
- Preparation: The substrate is cleaned and sometimes preheated to enhance the adhesion of the dip molding material.
- Dipping: The substrate is submerged into the liquid molding material, allowing a coating to form.
- Cooling and Solidification: After removal from the bath, the coated substrate is cooled, allowing the material to solidify and bond to the surface.
- Finishing: Post-processing steps such as trimming, drilling, or surface finishing may be necessary.
Advantages of Using Dip Molding Materials
Dip molding materials offer several distinct advantages that make them a highly attractive option for various applications, particularly in the electronics and medical fields:
1. Cost-Effectiveness
The dip molding process is generally less expensive than other manufacturing processes such as injection molding. This is primarily due to lower tooling costs and material waste.
2. Versatility
Dip molds can accommodate a variety of shapes and sizes. This flexibility allows for the customization of products tailored to specific requirements without a significant investment in new tooling.
3. Excellent Insulation Properties
In the electronics industry, effective insulation is crucial to ensure safety and performance. Dip molding materials such as PVC and TPE provide exceptional insulation, making them ideal for cable coatings and connectors.
4. Durability
Dip molded products tend to withstand a range of environmental conditions, making them suitable for both indoor and outdoor applications. Their resistance to chemicals, abrasion, and temperature variation adds to their longevity.
5. Biocompatibility
In the medical supply sector, materials such as liquid silicone rubber are favored for their biocompatibility. This property is essential for devices that come into contact with bodily fluids, as it minimizes the risk of adverse reactions.
Dip Molding Applications in Electronics
The electronics industry has significantly benefited from the incorporation of dip molding materials. Here are some key applications:
- Cable Insulation: Dip molded coatings for cables offer unrivaled protection against moisture, dirt, and other environmental factors.
- Connector Coatings: Coating electronic connectors with dip molding materials enhances their performance and longevity
- Tool Handles: Tools with dip molded rubber handles provide better grip and reduce fatigue during extended use.
Dip Molding Applications in Medical Supplies
In the medical field, the demand for high-quality, reliable products is paramount. Dip molding materials meet these demands through various applications:
- Medical Device Enclosures: Devices that require protection from contamination often utilize dip molded enclosures.
- Biocompatible Seals: Seals made from LSR protect sensitive electronic components in medical devices, ensuring functionality over time.
- Customizable Dosing Devices: Dip molding enables the creation of user-friendly dosing syringes and dispensers.
Future Trends in Dip Molding Materials
The evolution of dip molding materials is ongoing, shaping the future of industries such as electronics and medical supplies. Some trends to watch for include:
1. Sustainability
With the increasing emphasis on sustainability, manufacturers are exploring bio-based and recyclable dip molding materials. This shift will not only minimize environmental impact but also appeal to eco-conscious consumers.
2. Smart Materials
Integrating smart technologies into dip molded components may enhance functionality. Sensors and other electronic components can be embedded into molded materials, providing advanced features for both electronics and medical applications.
3. 3D Printing and Dip Molding Synergy
The intersection of 3D printing and dip molding could revolutionize the manufacturing process, allowing for rapid prototyping and complex designs that were previously unattainable.
The Competitive Edge: Nolato's Expertise in Dip Molding
Nolato is a leader in the field of dip molding, particularly in the sectors of electronics and medical supplies. Their commitment to innovation ensures that they remain at the forefront of dip molding technology. Key aspects of their expertise include:
- Advanced Material Research: Nolato continuously explores and develops new materials that enhance the performance of dip molded products.
- Customization: Their capability to provide tailored solutions allows clients to meet unique product specifications effectively.
- Quality Assurance: Rigorous testing and quality control ensure that all dip molded products meet industry standards and exceed expectations.
Conclusion
In summary, dip molding materials are an essential component in the manufacturing processes of both the electronics and medical supply industries. Their versatility, cost-effectiveness, and ability to meet rigorous standards position them as a preferred choice in numerous applications. Companies like Nolato continue to lead the way, ensuring that innovation and quality remain at the heart of dip molding advancements.
As industries evolve, the significance of dip molding is sure to grow, paving the way for new techniques and applications. Embracing these materials is not just a step forward; it is a leap towards a more efficient and sustainable manufacturing landscape.