The Importance of Refrigeration Equipment in Cold Chain Logistics
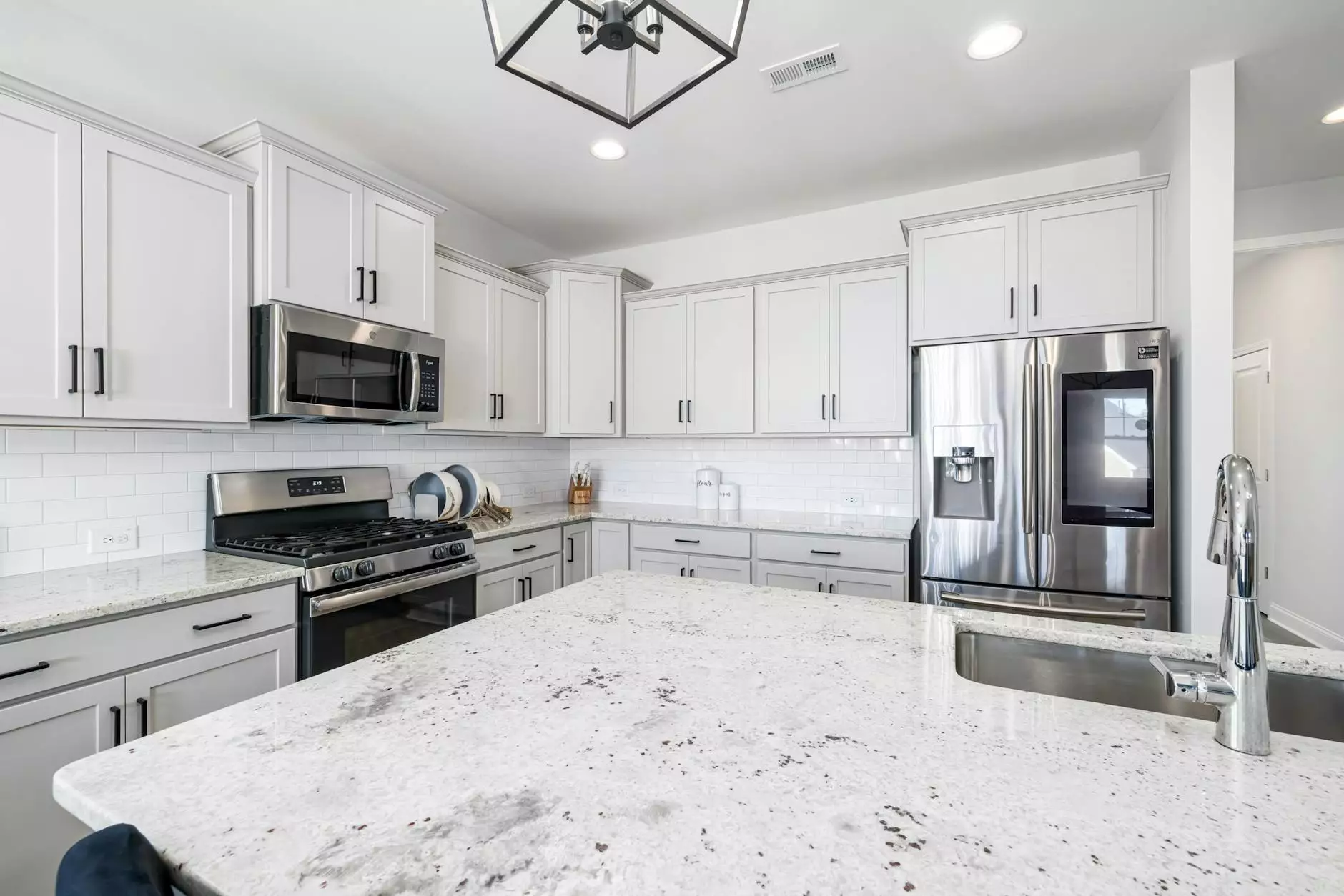
In an ever-evolving marketplace where consumer expectations are high, maintaining the integrity of products during storage and transportation is paramount. This is where cold chain logistics plays a pivotal role. A significant aspect of cold chain logistics is the use of refrigeration equipment, which ensures that temperature-sensitive products remain fresh and safe from spoilage. This article delves into the importance of refrigeration equipment in the cold chain process, how it can benefit businesses, and best practices to optimize cold chain operations.
Understanding Cold Chain Logistics
Cold chain logistics refers to the temperature-controlled supply chain that is crucial for transporting perishable goods, such as food, pharmaceuticals, and chemicals. A properly managed cold chain maintains an unbroken journey from point of manufacture to the final customer, ensuring quality and safety. The essential components of a cold chain include:
- Refrigeration Equipment: Units such as refrigerated trucks, storage facilities, and portable containers.
- Temperature Monitoring: Systems that provide real-time data on temperature and humidity levels.
- Efficient Transportation: Strategies for minimizing time spent in transit while adhering to regulatory requirements.
The Role of Refrigeration Equipment
Refrigeration equipment is the backbone of cold chain logistics. Its primary function is to maintain the required temperature for sensitive products throughout the supply chain. Here’s how refrigeration equipment contributes to various sectors:
1. Food and Beverage Industry
The food industry relies heavily on refrigeration to ensure the safety and quality of food products. Perishable items like meat, dairy, fruits, and vegetables require specific temperature conditions to prevent bacterial growth and spoilage. The use of refrigeration equipment ensures:
- Extension of Shelf Life: Products remain fresh for longer periods.
- Reduced Waste: Minimizing losses due to spoilage helps businesses retain profit.
- Compliance with Health Standards: Meeting food safety regulations protects consumer health and keeps businesses credible.
2. Pharmaceutical Sector
In the pharmaceutical industry, maintaining proper temperature controls is critical for medications and vaccines. Failure to do so can render products ineffective or dangerous. Refrigeration equipment plays a crucial role by:
- Protecting Product Potency: Ensuring that medications remain effective during transit.
- Meeting Regulatory Requirements: Compliance with FDA and other regulations safeguarding public health.
- Enhancing Trust: Reliable temperature controls establish customer confidence in pharmaceutical products.
3. Chemical and Industrial Applications
Many industrial products also require refrigeration to preserve quality. Chemicals can be highly sensitive to temperature changes, necessitating precision in storage and transport. The proper refrigeration equipment helps in:
- Ensuring Stability: Keeping chemicals within designated temperature ranges to maintain stability.
- Enhancing Safety: Reducing the chances of hazardous reactions due to temperature variations.
- Preventing Financial Losses: Protecting investments in valuable raw materials and finished goods.
Key Types of Refrigeration Equipment
Choosing the appropriate refrigeration equipment is crucial for effective cold chain management. Here are the most common types of refrigeration systems used within cold chain logistics:
1. Refrigerated Trucks
Refrigerated trucks or reefer trucks are essential for transporting goods over long distances while maintaining refrigeration standards. They are equipped with temperature-controlled compartments that can be monitored during transit. Key features include:
- Insulated Walls: Minimize temperature fluctuations during transport.
- Advanced Temperature Controls: Allow drivers to set and monitor specific temperature requirements.
- GPS Tracking: Provides real-time visibility into freight conditions and locations.
2. Walk-in Coolers and Freezers
Walk-in coolers and freezers are large storage units allowing for bulk storage of temperature-sensitive goods. These facilities are crucial for warehouses and distribution centers. Their benefits include:
- Large Capacity: Ideal for businesses dealing with high volumes of products.
- Energy Efficiency: Modern walk-in units are designed to be energy-efficient, reducing operational costs.
- Customizable Temperatures: Users can adjust settings to meet the requirements of various products.
3. Portable Refrigeration Units
Portable refrigeration units provide flexibility for businesses that need cold storage solutions on the go. They are essential for events or situations where temporary cooling is required. Advantages include:
- Mobility: Can be easily transported to different locations as needed.
- Versatility: Ideal for both short- and long-term storage options.
- Cost-Effective: Useful in reducing overhead costs of permanent refrigeration installations.
Best Practices for Optimizing Cold Chain Operations
To enhance cold chain efficiency and reliability, businesses must adopt best practices surrounding refrigeration equipment and logistics. Here are several strategies:
1. Implement Robust Temperature Monitoring Systems
Utilizing temperature monitoring systems is vital for ensuring compliance and product safety. Modern solutions allow for:
- Real-Time Tracking: Monitor temperatures continuously throughout the journey.
- Alerts and Notifications: Immediate alerts for any deviations from the desired temperature range.
- Data Logging: Keeping records to ensure proper compliance with health regulations.
2. Conduct Regular Maintenance Checks
Regular maintenance of refrigeration equipment ensures optimal performance and reduces the risk of equipment failure. Scheduled checks should include:
- Inspection of Seals and Insulation: Prevent cold air leaks which can raise temperatures inside storage units.
- Cleaning Condenser Coils: Ensure efficient operation and energy consumption.
- Testing Backup Systems: Verify that backup power or cooling systems are functional.
3. Train Employees in Cold Chain Protocols
An informed workforce is essential for maintaining cold chain integrity. Regular training should cover:
- Proper Loading Techniques: Avoiding temperature spikes during product loading and unloading.
- Handling Procedures: Instructing employees on how to handle temperature-sensitive goods properly.
- Emergency Protocols: Implementing steps to take in the event of temperature fluctuations.
4. Partner With Trusted Cold Chain Providers
Collaborating with reputable cold chain logistics providers can significantly enhance service quality. Look for partners that offer:
- Accreditation: Certifications from recognized organizations validating their operations.
- Advanced Technology: State-of-the-art refrigeration equipment and monitoring systems.
- Experience: A proven track record in managing cold chain logistics effectively.
Conclusion
In summary, refrigeration equipment is a pivotal component of cold chain logistics, especially for industries relying on temperature-sensitive products. Implementing effective cold chain practices not only helps in preserving product integrity but also builds consumer trust and complies with regulatory standards. Businesses that invest in the right refrigeration solutions and practices, including partnering with experts in the field, stand to gain significant advantages in this competitive landscape.
Visit first-coldchain.com for more insights on the latest refrigeration equipment and cold chain solutions.
https://www.first-coldchain.com/