The Power of Injection Molded Plastics in Business Growth
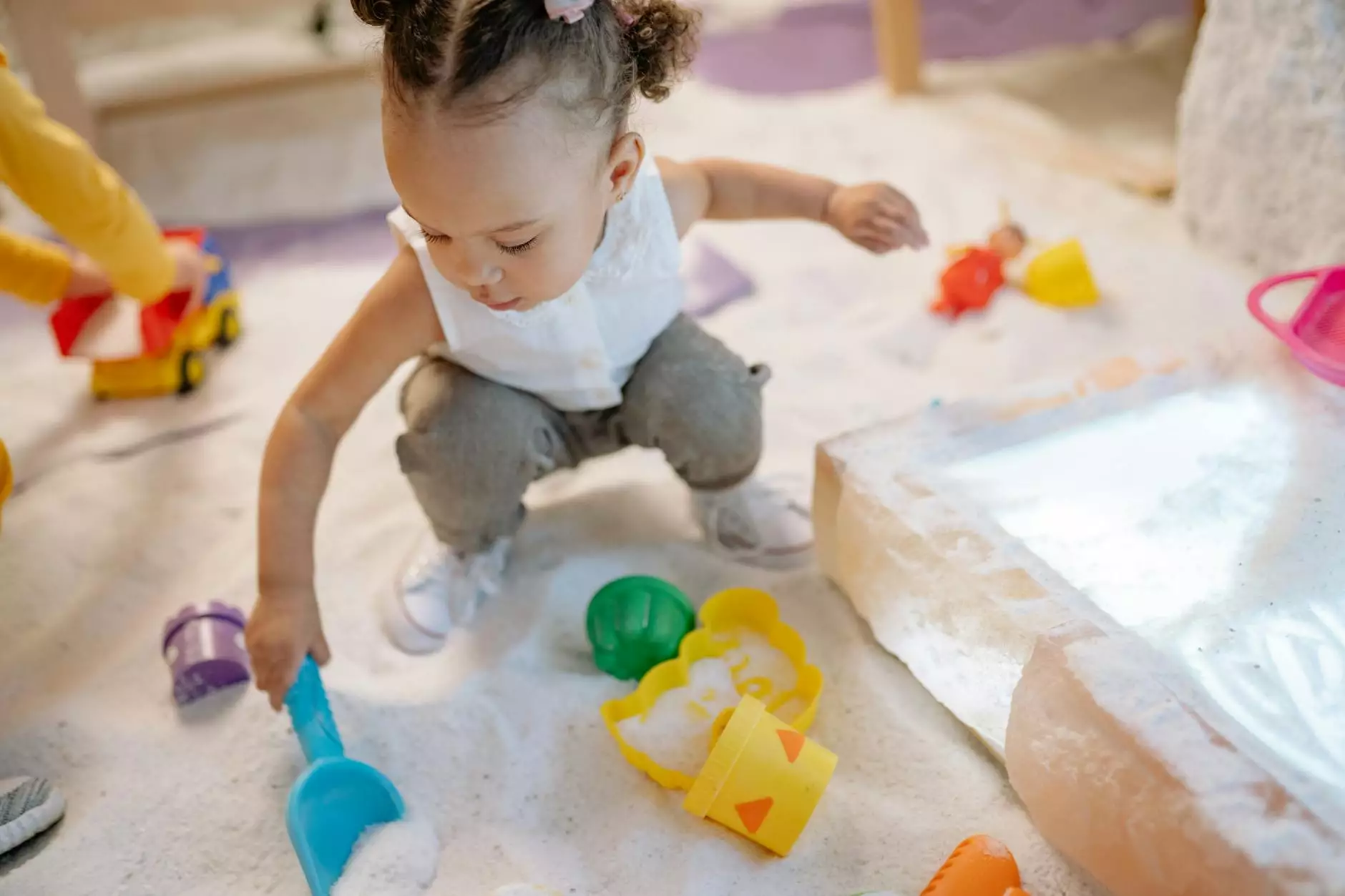
In today's highly competitive market, companies are constantly seeking innovative solutions to improve efficiency, reduce costs, and enhance product quality. One method that has become increasingly popular is injection molded plastics, a versatile manufacturing process that offers numerous advantages across various industries. In this article, we'll delve into the significance of injection molded plastics, the benefits they provide, and how they can transform your business operations.
What is Injection Molding?
Injection molding is a manufacturing process used for producing parts by injecting molten material into a mold. This technique is prevalent in the production of plastic components, where the mold defines the final shape and texture of the product. The process begins with the melting of the resin, which is then injected into a prepared mold at high pressure. Once cooled and solidified, the mold opens to release the finished part.
Key Components of the Injection Molding Process
- Material Selection: The choice of plastic material is crucial, as it affects the strength, durability, and appearance of the finished product.
- Mold Design: The mold must be carefully designed to facilitate easy injection and removal of parts while ensuring high precision.
- Injection Machine: Modern machines offer advanced control for temperature, pressure, and speed, greatly enhancing production efficiency.
- Quality Control: Implementing rigorous quality checks throughout the process ensures that the finished products meet industry standards.
Advantages of Using Injection Molded Plastics
The adoption of injection molded plastics can offer several substantial benefits for businesses, particularly in the manufacturing and fabrication sectors. These advantages include efficiency, cost-effectiveness, and superior design flexibility.
1. Efficiency and Speed
One of the most significant benefits of injection molding is its speed. Large volumes of parts can be produced quickly, allowing businesses to meet high demand with minimal turnaround times. This efficiency is especially beneficial for companies that require a consistent supply of parts for assembly lines or distribution.
2. Cost-Effectiveness
Though the initial investment in molds may be substantial, the long-term savings cannot be overstated. Injection molding drastically reduces material waste compared to other manufacturing methods. Additionally, the durability of injection molded products leads to lower replacement rates, saving businesses money in the long run.
3. Design Flexibility
Injection molding supports complex designs that may otherwise be challenging or impossible to achieve with other manufacturing processes. The technique allows manufacturers to create intricate shapes, fine details, and varied textures, enhancing the overall aesthetic and functional attributes of products.
4. Material Variety
A wide range of materials can be used in the injection molding process, including various types of thermoplastics, thermosets, and even biodegradable options. This variety ensures that businesses can select the most suitable material for their specific application, whether it requires flexibility, strength, heat resistance, or other properties.
5. Consistency and Quality
Injection molding provides remarkable consistency in production, resulting in minimal variance between individual parts. This consistency is crucial for industries such as automotive and electronics, where precision is paramount. Advanced quality control measures can be integrated into the process to further enhance product reliability.
Applications of Injection Molded Plastics
Injection molded plastics are incredibly versatile and find applications in various industries. Here are some notable examples:
1. Automotive Industry
The automotive sector relies heavily on injection molded plastics for components such as dashboards, bumpers, and interior fittings. The ability to produce lightweight and durable parts that can withstand harsh conditions makes this manufacturing process ideal for automotive applications.
2. Consumer Goods
Everyday items, from kitchen utensils to electronic housings, often utilize injection molded plastics. This method allows for the mass production of high-quality consumer products with appealing designs.
3. Medical Devices
In the healthcare field, injection molded plastics are used for producing essential devices such as syringes, surgical instruments, and diagnostic equipment. The process meets strict regulatory standards, ensuring the safety and reliability of medical products.
4. Packaging Industry
Injection molded packaging solutions, such as containers and closures, offer enhanced durability and protection for various products, making it a preferred choice for manufacturers and retailers alike.
Combining Injection Molded Plastics with Metal Fabrication
As a business involved in both metal fabrication and injection molded plastics, you can leverage the synergy between these two processes to create superior products. Combining the strength of metals with the lightweight, flexible nature of plastics can result in innovative solutions that meet diverse consumer needs.
1. Hybrid Components
Using both injection molded plastics and metal fabrication allows for the creation of hybrid components. These parts can take advantage of the unique properties of both materials, resulting in products that are not only strong but also lightweight and cost-effective.
2. Enhanced Product Design
Integrating metal structures with injection molded plastic can enhance product designs by allowing for greater complexity and functionality. Examples include housing for electrical components that require both structural support and insulation.
Choosing a Partner for Injection Molded Plastics
When considering the integration of injection molded plastics into your business model, selecting the right manufacturing partner is crucial. Here are some key factors to consider:
1. Experience and Expertise
Look for a partner that has extensive experience in both injection molding and metal fabrication. Their expertise will ensure that they understand the challenges and nuances of both processes, allowing for seamless integration.
2. Quality Assurance Practices
Choose a manufacturer that prioritizes quality control throughout the production process. Certifications such as ISO can be indicators of their commitment to maintaining high standards.
3. Technological Capabilities
Investing in advanced machinery and technology plays a significant role in the efficiency and quality of the injection molding process. Ensure that your partner utilizes the latest equipment and software to optimize production.
4. Customization Options
Your manufacturing partner should offer customizable solutions tailored to your specific needs. This flexibility will enable you to create unique products that stand out in the market.
Future Trends in Injection Molded Plastics
The future of injection molded plastics is promising, with several trends emerging that could further revolutionize the industry:
1. Sustainable Practices
As environmental concerns grow, the demand for sustainable practices in manufacturing becomes more critical. Innovations in bio-based plastics and recycling technologies will significantly influence the future of injection molding.
2. Smart Manufacturing
The shift towards smart manufacturing, driven by advancements in IoT and automation, is expected to enhance production processes. Injection molding facilities incorporating smart technologies will achieve higher efficiency and reduced downtime.
3. Advanced Materials
Research into new materials that can withstand higher temperatures and pressures will enable the development of even more resilient products. The ongoing exploration of composites containing plastic and other materials promises exciting advancements.
Conclusion
In conclusion, the use of injection molded plastics presents a wealth of opportunities for businesses aiming to streamline production, reduce costs, and drive innovation. By harnessing the efficiencies of this manufacturing process, companies in various sectors, including metal fabricators, can not only enhance their product offerings but also secure a position of strength in a competitive marketplace. As you look to the future, consider integrating injection molded plastics into your operations and partnering with expert manufacturers to unlock new possibilities for growth.
For more information about injection molded plastics and how they can benefit your business, visit Deep Mould.