Understanding Industrial Vacuum System Design
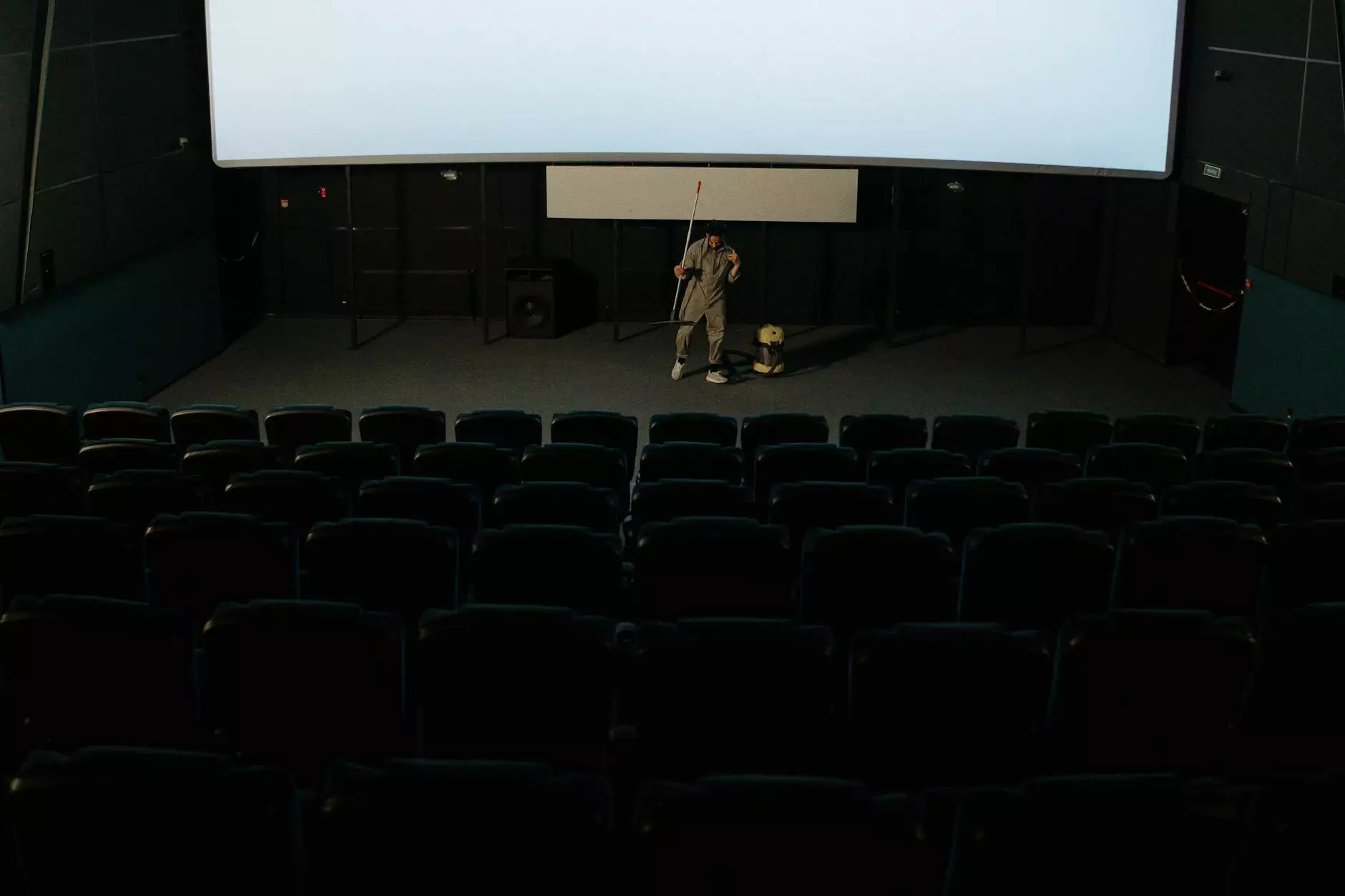
In today’s industrial landscape, efficiency and cleanliness are paramount. This is where industrial vacuum system design plays a critical role. Innovative vacuum systems have empowered industries to improve productivity and reduce downtime while ensuring a safer working environment.
The Importance of Industrial Vacuum Systems
Industrial vacuum systems are indispensable in various sectors, from manufacturing to food processing. These systems are essential for:
- Removing dust and debris
- Ensuring compliance with health and safety standards
- Enhancing workplace cleanliness
- Improving product quality
As industries evolve, the demand for efficient vacuum systems increases. A well-designed industrial vacuum system can lead to significant savings and improved operational efficiency.
Key Components of Industrial Vacuum Systems
A successful industrial vacuum system design comprises several core components, each serving a unique purpose. Understanding these components helps in appreciating their impact on system performance:
1. Vacuum Pumps
Vacuum pumps are the heart of any vacuum system. They create the suction needed to remove particles from the air. There are different types of vacuum pumps, including:
- Positive displacement pumps - These pumps capture air using a mechanical chamber.
- Kinetic pumps - Employs the motion of rotating blades to accelerate air and create a vacuum.
The choice of vacuum pump significantly influences the system's efficiency and effectiveness, depending on the material and environment in which they operate.
2. Filtration Systems
Effective filtration is crucial for maintaining air quality. Airborne contaminants can severely impact both operational efficiency and worker health. Typical filtration solutions include:
- HEPA Filters - Highly effective at capturing small particles.
- Pre-filters - Extend the life of HEPA filters by capturing larger debris first.
- Electrostatic filters - Utilize static electricity to attract dust and particles.
The right combination of filters will ensure that the air discharged is clean, thus creating a safer working environment.
3. Hoses and Accessories
Hoses are essential for connectivity between the vacuum pump and the workspace. Well-designed hoses can prevent blockages and ensure efficient suction. Accessories like tool attachments can further enhance operational flexibility.
Design Considerations in Industrial Vacuum Systems
Designing an industrial vacuum system requires a thorough understanding of specific operational needs. Here are some fundamental considerations:
1. Application Requirements
Different industries have varying needs. A vacuum system designed for woodworking will differ drastically from one used in food manufacturing. It is crucial to analyze:
- Type of materials being handled
- Volume of air to be evacuated
- Specific cleanliness standards
2. Space Constraints
The available space for the system often dictates design choices. Compact designs may need to incorporate multiple functions in one unit to optimize space without sacrificing performance.
3. Energy Efficiency
With rise in energy costs, designing energy-efficient industrial vacuum systems is imperative. Integrating features like variable frequency drives can significantly reduce energy consumption while maintaining performance.
Applications of Industrial Vacuum Systems
The applications of industrial vacuum systems are vast and varied. Here are some significant uses:
1. Manufacturing and Assembly
In manufacturing environments, vacuum systems are used for:
- Collecting chips in machining operations
- Removing dust and debris during assembly
- Transporting materials in production lines
2. Food Processing
Food safety is paramount, and vacuum systems help achieve this by:
- Removing contaminants from production areas
- Assisting in dough pumps and other food transport needs
- Maintaining ingredient quality during processing
3. Pharmaceutical Industry
In the pharmaceutical sector, ensuring cleanliness is essential to avoid contamination. Industrial vacuum systems can be designed to handle:
- Fine powders
- Chemical spills
- General cleaning in sterile environments
Benefits of Properly Designed Industrial Vacuum Systems
Designing a tailored industrial vacuum system leads to an array of benefits for businesses, including:
1. Enhanced Efficiency
A well-designed system optimizes suction and minimizes downtime, leading to increased efficiency across operations.
2. Improved Safety
By maintaining a clean work environment, businesses are less liable for accidents related to spills and debris, ensuring employee safety.
3. Cost Savings
Investing in a high-quality vacuum system will lower long-term operational costs. Effective filtration reduces maintenance needs and extends equipment lifespan.
4. Compliance with Regulations
Industries are often required to adhere to strict cleaning regulations. A well-designed vacuum system can ensure compliance with health and safety standards, avoiding penalties.
Future Trends in Industrial Vacuum Systems
The realm of industrial vacuum system design is continually evolving. Significant trends include:
- Automation: The integration of smart technology allows for real-time monitoring and control over vacuum systems.
- Energy Efficiency: Focus on sustainable designs that lower energy consumption and emissions.
- Modularity: Design systems that are easily adjustable or expandable based on changing operational needs.
Conclusion
In conclusion, industrial vacuum system design is a critical aspect of maintaining efficiency and safety in various industries. Businesses like TMM are at the forefront, offering innovative solutions tailored to specific needs. A well-implemented vacuum system not only enhances productivity but also ensures compliance with industry standards. As technology advances, the future of industrial vacuum systems promises to bring even more efficiency and effectiveness, supporting businesses in their quest for excellence.